Hydraulic Woes
contributed by Mike Bowes
Before I start into
this tale of another problem with the Seawind hydraulic system, I would like to
say that, overall I am pleased with the design and performance of the system as
supplied by S.N.A. The system is compact, lightweight, simple in operation, and
works well most of the time. Further, I think the components are of durable
design and, in our application, should give years of reliable service. We set up
the system to operate at just over 50% of its rated pressure capacity. The pumps
normally see life as tilt-trim motors on marine out-drives and raising and
angling snowplows in the great white north.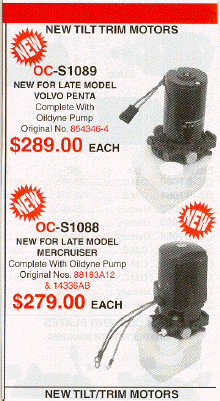
Having said that, if
I were to name one particular weakness in the entire system, it would be
vulnerability to dirt. Contaminants in the hydraulic oil can wreak havoc with
your solenoid activated selector valves, causing them to jam or leak-by
excessively. Fortunately, they are relatively easy to disassemble and clean. Use
metric hex keys to accomplish the job. Why not disassemble one some day, at your
leisure, for some practical experience? The little spool valve can go back into
the bore either way, and make sure the depression in the washers faces out to
engage the base of the spring. It is essential to install an in-line filter at
the pump, like the little Arrow unit supplied by S.N.A. from day one of
operation. I recommend blowing out all lines and fittings with compressed air
prior to assembling the system parts for the final time.
You may recall me
writing about a severe hydraulic problem on N11PR- Turned out to be two of the
three gear actuating cylinders were passing pressure by the seals, internally.
We wasted much time isolating the two defective cylinders. Well folks, here is a
brand new problem that we just had on Arnie Tanzman’s N711AT. In six years of
working with these systems I had never previously seen this one. Hopefully, the
following explanation will save someone else some time in the future.
Essentially the
system was working OK and correctly except the gear was a little slow to come
up, especially the right main gear leg. I bumped the system pressure up to about
1700 psi and that really didn’t help. So we changed out the right main gear
actuator cylinder. That made no difference. We changed out all of the solenoid
selector valves, one at a time, starting with the gear. That made no difference.
As we worked on the system we noticed an anomaly. With the hydraulic pump
switched off, you should be able to exercise the flaps to bleed off the residual
pressure in the system prior to cracking open a line or removing a solenoid
valve. On this system we could not get the residual to drop below about 400 to
500 psi. This is definitely not normal! It should go to zero.
We were baffled, but
reasoned that somehow the pump itself was retaining some pressure on the
return-to-the-tank side. In effect, the high pressure side of the system was
having to work against a certain amount of lower pressure being retained on the
other side of the cylinder seals. That certainly makes for sluggish gear
operation, wouldn’t you think? Now, taking the Oildyne pump apart is another
one of those things on the list of Stuff I Won’t Do. Instead, we swapped out
the pump entirely and, Lo and Behold, the problem was gone! Proof to me that
this problem was within the internal workings of the pump. I have forwarded the
pump to Mike Pastelak, who has, I understand, sent it on to their distributor
for testing and evaluation. I fully expect it will be diagnosed as having some
rare internal defect. As of this writing I have not received confirmation of
this fact.